High Density Metals are made possible by Powder Metallurgy techniques. The process is a mixture of tungsten powder with nickel, iron, and/or copper and molybdenum powder, compacted and liquid phase sintered, giving a homogeneous structure with no grain direction. The result is a very high density, machinable material with unique physical properties.
TYPICAL APPLICATIONS
Weights and Counterbalances for aircraft control surfaces and rotor blades, guidance platforms, balancing of flywheels and turbines, vibration damping governors, fuse masses, and weights for self-winding watches. Because of the physical properties of high density metal, it is often used as both a weight and structural member.
CRANKSHAFT BALANCING — Used extensively to balance crankshafts in high performance engines. Individual weights are stocked.
RADIATION SHIELDlNG — Tungsten alloys are used for radioactive source containers, gamma radiography, shields and source holders for oil well logging and industrial instrumentation; for collimators and shielding in cancer therapy machines and syringe protection for radioactive injections, There is no licensing required for tungsten alloy materials. It is stable at high temperatures and 1/3 less material than lead can be used for the same energy absorption effectiveness. High density tungsten alloys are used wherever radioactivity has to be controlled mid directed.
ROTATING INERTIA MEMBERS — Material Is used for gyro rotors, fly wheels, and rotating members for governors. Because of its unique physical properties, this material can be rotated at extremely high speeds.
ORDNANCE COMPONENTS — In spheres, cubes. and projectile shapes. these materials are used for hypervelocity armor penetrating applications. Properties such as elongation, ultimate tensile strength, arid hardness can be varied by manufacturing technique and additives.
BORING BARS AND GRINDING QUILLS — The standard for vibration free machining and grinding has been established by Chatter Free and Super Chatter Free materials. It’s used where rigidity and minimum vibration are critical Heavier cuts, Longer tool life, end a better finish result when using Chatter Free materials. Tool extensions of up to 9-1 are possible depending on the diameter. Tools run cooler because of the high thermal conductivity, and you can braze directly to material without affecting its physical properties.
These materials are often used in place of tungsten carbide boring bars because it has a higher density, is readily machinable, less prone to chipping and breakage, and both material and finishing casts are less. See our technical brochure Chatter Free and Super Chatter Free materials.
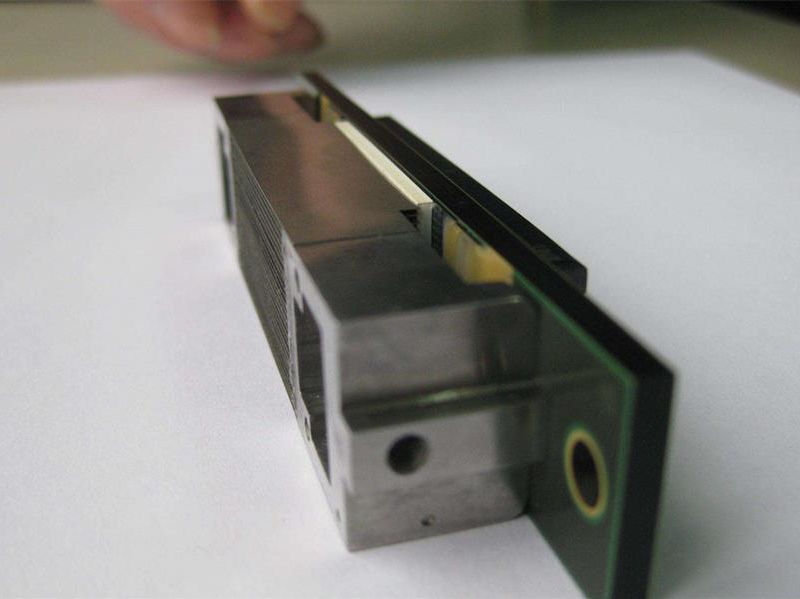
Post time: Jul-29-2022